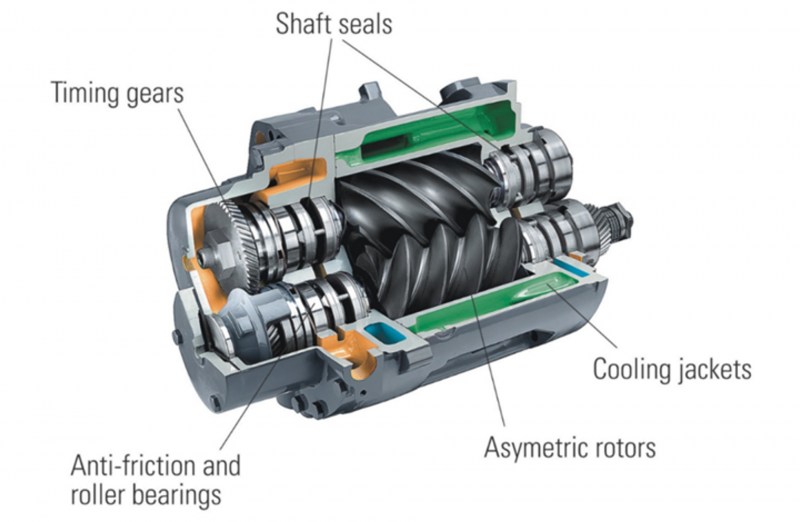
Scopri su Infoimpianti le diverse tipologie di compressori frigorifero, come compressori a vite, compressori scroll e le turbomacchine. Di seguito la quinta parte del corso per frigoristi e i principi della termodinamica che regolano il funzionamento dei frigoriferi.
Oltre il compressore alternativo: altri sistemi di compressione
Il compressore alternativo, diffusissimo nel settore delle potenze piccole e medie, non è sempre vantaggioso per i grandi impianti, nei quali talvolta si fa ricorso a macchine basate su principi di funzionamento diversi. Tra i sistemi che descriviamo, il primo trova applicazione anche nei compressori ermetici.
Il compressore rotativo a palette è basato sul disassamento di un rotore cilindrico fatto ruotare all’interno di una cavità cilindrica di diametro maggiore. Nel rotore sono inseriti segmenti rettilinei di tenuta (o palette) i quali si muovono entro scanalature radiali sotto la spinta di molle, e sono quindi in grado di seguire il profilo della camera. Lo spazio compreso tra due pareti convergenti e il loro punto di tangenza si riduce a ogni giro comprimendo il gas sino a farlo uscire dalla, valvola di scarico.
Il compressore a pistone rotante è una variante del compressore rotativo, in cui l’elemento premente è un anello che gira eccentricamente entro una camera di diametro uguale a quello della sua orbita. La tenuta è assicurata da una sola lama, inserita in una scanalatura del corpo della macchina.
Compressori a rapporto di compressione intrinseco
Fanno parte di questa categoria tutti quei compressori privi di valvole che incrementano la pressione mediante la riduzione progressiva del volume all’interno del quale è alloggiato il refrigerante stesso. Se a titolo di esempio viene aspirato alla pressione di evaporazione un volume pari a 8, questo verrà scaricato quando il volume si sarà ridotto di otto volte, ovvero quando si sarà ridotto a 1. Per quanto detto si evince che la pressione di scarico deve essere sempre superiore a quella di alta pressione, e quindi ci si trova in presenza di un lavoro di compressione superiore a quanto dovuto. Fanno parte di questa categoria di compressori i compressori a vite e i compressori scroll.
Compressori a vite
I compressori vite fanno parte della famiglia dei cosiddetti compressori a spostamento positivo, ovvero di quel tipo di compressori volumetrici che, per incrementare la pressione del refrigerante aspirato, agisce sulla riduzione del volume, come avviene per la maggioranza di tutti i compressori, eccezion fatta per quelli definiti con il termine “dinamici”. La differenza che caratterizza questi compressori da quelli alternativi, si concretizza nel fatto che la compressione avviene tramite un movimento rotatorio e non alternativo così come avviene in quelli a pistone, nei quali il volume del gas è ridotto tramite uno o più pistoni che si muovono alternativamente ed in modo coassiale nel cilindro, o nei compressori a membrana, dove la variazione del volume è prodotta dalla flessione di una pellicola elastica. Nei compressori volumetrici rotativi, la compressione è il risultato della riduzione del volume racchiuso tra elementi rotanti, come avviene ad esempio tra le superfici elicoidali delle viti di un compressore a doppia vite. Un’ulteriore suddivisione, che spesso viene fatta parlando di queste macchine, la troviamo nel numero di rotori impegnati; compressori ad una singola vite possono essere, a titolo di esempio:
– a paletta scorrevole;
– a vite singola;
– ad anello liquido;
– scroll.
Mentre i compressori a due viti possono essere:
– a lobi rotanti;
– a viti gemelle o a doppia vite.
In questo articolo trattiamo il compressore a viti gemelle. Un compressore a doppia vite è costituito da una coppia di alberi opportunamente sagomati e alloggiati in un involucro fisso detto statore (o carcassa) in cui il profilo sagomato della superficie esterna della vite detta rotorica, e quella interna, detta trascinata, costituiscano, tra loro, dei volumi di grandezza decrescente durante la rotazione. Grazie ad un foro praticato sulla carcassa, questi volumi si aprono da un lato verso la linea di aspirazione in corrispondenza del medesimo rubinetto (o luce di aspirazione) con lo scopo di prelevare il fluido durante la fase di aspirazione; dall’altro lato sullo scarico al termine della compressione.
In questo caso si parla sempre di macchine a rapporto di compressione intrinseco, il che significa che il volume iniziale del gas aspirato si riduce, allo scarico, di “n” volte dipendendo solamente dalla forma costruttiva della macchina. Pertanto, la mancanza di valvole comporta l’inconveniente della impossibilità di adeguamento della pressione di mandata alle condizioni di pressione regnanti nell’ambiente di scarico. In altri termini, mentre nella macchina alternativa l’apertura e la chiusura della valvola di mandata ha luogo soltanto quando la pressione interna al cilindro è pari a quella dello scarico, in una macchina rotativa il valore della pressione è definito dalle caratteristiche geometriche dei vani per cui al variare della pressione richiesta dal circuito a valle, il fluido aspirato deve, all’uscita della macchina, espandersi o comprimersi istantaneamente a volume costante (al valore delle condizioni di scarico del circuito frigorifero) con conseguenti inevitabili irreversibilità.
Il compressore a vite si compone di due rotori di forma elicoidale ma di differenti geometrie, uno traente (generalmente il maschio) e l’altro condotto (generalmente la femmina), e gli assi di rotazione posti in parallelo. Il rotore maschio presenta una sezione lobata, mentre il rotore femmina è caratterizzato da un numero di cave sempre in numero superiore rispetto ai lobi del maschio. I rotori ruotano all’interno della carcassa senza avere nessun contatto con le pareti interne di quest’ultima grazie a precise tolleranze di lavorazione tra le parti mobili e le parti fisse della macchina. Lobi, cave e pareti dell’involucro, delimitano il volume della camera di compressione. Come già detto la compressione del gas si realizza mediante la progressiva riduzione del volume delle camere elicoidali situate tra i due rotori e tra i rotori e le pareti interne della cassa.
I compressori a doppia vite vengono classificati in due tipologie: compressori privi di olio lubrificante (o a secco) o compressori con iniezione di olio lubrificante (a bagno d’olio).
Nei compressori a doppia vite privi di olio lubrificante, non c’è miscelazione tra olio e fluido frigorigeno e, per impedire che i due rotori interferiscano tra di loro, il loro movimento è regolato da una coppia d’ingranaggi posti sui relativi assi di rotazione che sono collocati al di fuori della camera operativa. Affinché l’olio che lubrifica cuscinetti ed alberi non possa mai entrare in contatto con la camera operativa, su ogni albero sono poste delle idonee tenute che garantiscono, per un certo tempo, questa condizione. Per poter costruire macchine con tolleranze così ristrette, questi compressori che hanno un rendimento volumetrico migliore rispetto a quelli a bagno d’olio, sono inficiati da un costo d’acquisto maggiore e dallo svantaggio di dover provvedere, in qualche maniera, al raffreddamento dell’olio lubrificante. Oltre a ciò, per garantire un’idonea lubrificazione, occorre prevedere un serbatoio, un filtro e una pompa che assicuri un costante flusso di olio alle condizioni previste.
I compressori a doppia vite con iniezione di olio lubrificante o a bagno d’olio, al contrario, sono stati sviluppati in un secondo tempo per ridurre i problemi qui sopra citati. In questo caso un motore elettrico mette in rotazione il rotore maschio che a sua volta, ingranando con il rotore femmina lo pone, a sua volta, in rotazione. I due rotori non vengono mai in contatto l’uno con l’altro perché sono sempre separati da un film di olio che è costantemente pompato tra i lobi. In questo caso quando si parla di volume spostato occorrerà sempre tenere presente che una parte di esso è composto da olio lubrificante.
Comunque, la funzione dell’olio in questa applicazione è quella di:
– contenere l’incremento della temperatura del refrigerante durante la compressione;
– sigillare i trafilamenti;
– lubrificare il movimento dei rotori.
Una tale portata di olio richiede allo scarico del compressore un separatore di olio particolarmente efficiente, un suo eventuale sistema di raffreddamento, un filtro meccanico, un sistema di controllo sia del flusso che del livello dell’olio nel serbatoio in modo tale che il compressore si possa arrestare quando la lubrificazione diviene carente o assente. L’olio così trattato viene rimandato in aspirazione del compressore tramite un’apposita luce. Il rapporto di compressione intrinseco di queste macchine può andare normalmente da 5:1 fino a 15:1. Come già detto, la compressione del gas si realizza mediante la progressiva riduzione del volume delle camere elicoidali situate tra i due rotori e tra i rotori e le pareti interne della cassa.
Quando il compressore è in rotazione il gas entra dalla luce di aspirazione riempendo tutti gli spazi tra i lobi e tra lobi e carcassa. Lo spazio occupato s’incrementa, durante la rotazione, in lunghezza, mentre il punto di inserimento tra i lobi procede verso la luce di scarico. Quando lo spazio interlobare si è riempito di gas aspirato, la luce di aspirazione si chiude e termina la fase di immissione con una quantità definita di gas intrappolato nella macchina che viene compresso in quanto, proseguendo la rotazione, decresce il volume tra i lobi. Ad una posizione definita dei rotori infine, il gas compresso intrappolato raggiunge la luce di scarico ed inizia la fase di mandata che continua fino a che lo spazio tra i lobi si è interamente svuotato.
È importante capire come il compressore a doppia vite sia caratterizzato dall’alloggiamento in uno statore (carcassa) di una coppia di rotori elicoidali a lobi che ingranano tra di loro: la compressione è quindi ottenuta dalla rotazione di due viti elicoidali controrotanti. Ciascun passo dei due rotori a vite costituisce, di fatto, una camera di lavoro nella quale è contenuto il refrigerante.
Prendendo in considerazione una camera di lavoro alla volta, possiamo dire che ad un certo istante di tempo “t” la quantità di refrigerante racchiuso tra i due lobi sia prossima a zero. Procedendo con la rotazione del rotore maschio dopo un certo angolo, il volume della camera di lavoro è massimo e quella alle sue spalle è divenuta nulla. Le successive rotazioni portano avanti il refrigerante ma la riduzione del volume a loro disposizione genera una compressione dello stesso con un conseguente aumento della temperatura. Un’ulteriore rotazione, porta il frigorigeno alla massima compressione facendolo fuoriuscire dai lobi che, fino a quel punto, lo avevano intrappolato.
L’azione dei lobi, connessa alla loro rotazione, è del tutto simile a quella di una vite senza fine accoppiata ad una ruota elicoidale ma, in aggiunta, la loro forma è tale da garantire un’adeguata tenuta, sia tra i rotori che tra i rotori e la carcassa esterna. Le forze di attrito che si generano in questo processo tra i lobi devono essere limitate al massimo per poter minimizzare le perdite interne.
Rispetto ad altri compressori con spostamento positivo i compressori a vite presentano i seguenti vantaggi:
– non avendo parti in moto alterno (bielle, pistoni…ecc.), ma solamente due alberi bilanciati, possono operare in un campo di velocità più ampio rispetto a altri tipi di compressori;
– in secondo luogo, a differenza delle macchine a palette, le forze di contatto al loro interno sono basse, il che li rende molto affidabili;
– terzo e meno noto, a differenza delle macchine a pistoni, a spirale e a palette, tutte le linee di contatto di tenuta che definiscono i confini di ogni camera del vano, diminuiscono di lunghezza al diminuire delle dimensioni della camera di lavoro e la pressione, al suo interno, aumenta, questo riduce al minimo la fuoriuscita di gas dalla camera a causa di perdite durante il processo di compressione o di espansione.
Come già accennato la tenuta tra le viti e la tenuta tra viti e carter è una condizione indispensabile affinché la macchina possa disporre di un rendimento volumetrico accettabile. Ne consegue che l’efficienza del compressore dipende sia dal profilo del rotore che dalle distanze tra i rotori e tra i rotori e l’alloggiamento del compressore.
Un altro punto importante è la corretta progettazione del rotore, e questo fatto presuppone che sin dalla progettazione si possa prevedere con precisione gli effetti sulle prestazioni della modifica di qualsiasi parametro di progettazione, come ad esempio il gioco, la forma del profilo del rotore, la posizione e la velocità di iniezione dell’olio o del fluido e la velocità del rotore.
Compressori Scroll
Questo compressore a spirale utilizza due alette a spirale una dentro l’altra, di cui una fissa e una con movimento planetario senza rotazione, in modo da comprimere i fluidi. In seguito al loro movimento reciproco e grazie al ridotto gioco tra le due spirali, intrappolano e pompano o comprimono sacche di fluido tra i rotoli. Questi compressori hanno un elevato rendimento volumetrico. Il principio su cui si basa il funzionamento del compressore scroll è molto più semplice di quello che si pensa. Protagoniste sono due spirali di archimede inserite una dentro l’altra, delle quali una è bloccata nella parte superiore e l’altra è inserita subito sotto di essa, guidata da un eccentrico posto sull’albero motore che, ruotando la fa orbitare — non girare — all’interno di quella superiore.
La spirale orbitante nel compiere il suo moto, fa aumentare il volume fra le due spirali, nella posizione più lontana dal centro “estremità” mentre, contemporaneamente, diminuisce il volume verso il centro; perciò nella periferia c’è aspirazione, e via via che i volumi si riducono verso il centro, c’è compressione fino all’espulsione che avviene al centro delle spirali. Quindi il percorso del fluido refrigerante va dalle due aperture di aspirazione esterne e opposte fino al centro della spirale fissa nel quale raggiunge la massima compressione. Tale processo avviene in modo uniforme privo di vibrazioni. Sia l’aspirazione che avviene nell’estremità delle spirali, sia la compressione che si realizza verso l’interno e la mandata al centro, sono omogenee.
Turbomacchine
I compressori scroll, vite e rotativi a palette, sono macchine volumetriche, mentre i compressori centrifughi sono turbomacchine. Il principio di funzionamento è totalmente diverso. Nei compressori volumetrici la pressione aumenta perché si riduce il volume della camera di compressione tra ingresso e uscita del refrigerante, mentre nei turbocompressori non vi è riduzione del volume della camera di compressione, ma una variazione dinamica della direzione e della velocità del flusso di refrigerante. In particolare, la variazione di pressione avviene perché varia il momento della quantità di moto del refrigerante. Una prima sostanziale differenza nel comportamento è data dalla variazione del salto di pressione (o prevalenza) al variare del numero di giri. Mentre nei compressori volumetrici il salto di pressione ottenibile è sostanzialmente indipendente dalla velocità di rotazione, nelle turbomacchine il salto di pressione si riduce con il quadrato del numero di giri. Di conseguenza, mentre nei compressori volumetrici il numero dei giri può essere ridotto a prescindere dal salto di pressione richiesto, nei turbocompressori la riduzione è possibile solamente se vi è una contemporanea riduzione del salto di pressione. La portata di refrigerante varia invece linearmente con il numero di giri per entrambe le tipologie di compressore.
Il compressore centrifugo è costituito da una girante di turbina, che aspira il gas in prossimità del proprio asse e lo lancia per effetto centrifugo lungo una pista a chiocciola. L’efficienza del compressore centrifugo è legata ad alte velocità di rotazione, che rendono necessaria una trasmissione a ingranaggi per moltiplicare i giri forniti dal motore. Per contro, la macchina è priva di valvole.
Leggi anche:
Condividi l'articolo
Scegli su quale Social Network vuoi condividere