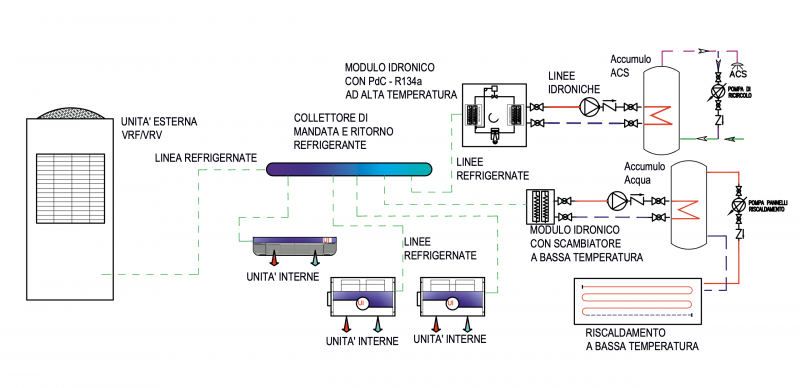
Un caso particolare di macchine che merita attenzione sono le pompe di calore ad espansione diretta (aria-aria e acqua-aria) a portata di refrigerante variabile, dette VRF e VRV. Questi sistemi VRF e VRV, acronimo inglese di Variant Refrigerant Flow oppure Variant Refrigerant Volume (usato da una sola casa costruttrice) sono in sostanza un sistema a pompa di calore ad espansione diretta di gas refrigerante a portata volumetrica variabile, in grado di collegare e gestire più unità interne rispetto ai sistemi multi-split presenti nel mercato.
Il sistema nasce a metà degli anni settanta e si sviluppa concettualmente in Giappone e Cina a fronte della crisi energetica del 1973. Le case più importanti di quei paesi negli anni ottanta cominciano a farsi notare in occidente. Il sistema prende piede in Europa commercialmente negli anni novanta. In Italia i termotecnici ne prendono consapevolezza e cominciano a progettare e installare sistemi VRF e VRV. Oggi il prodotto, per far fronte a tutte le necessità, oltre che essere commercializzato da numerose case provenienti da Cina, Giappone, India e altri paesi Orientali, è presente nel catalogo di molti produttori europei e in particolare italiani. Da sottolineare, comunque, come molte case italiane siano state assorbite da produttori orientali che conseguentemente hanno iniettato, all’interno di queste aziende, il loro know how ed esperienza nel campo dell’espansione diretta. I sistemi VRF e VRV in pompa di calore o a recupero di calore rappresentano quindi un sistema impiantistico evoluto, dal punto di vista meccanico elettrico ed elettronico, idoneo a rispondere alle esigenze di comfort individuale e di funzionalità impiantistica, presentando molti pregi in tal senso.
L’acronimo VRF e VRV come detto – Variant Refrigerant Flow oppure Variant Refrigerant Volume (Daikin) – deriva in sostanza dalla logica di regolazione della potenza frigorifera che avviene modulando di continuo la portata volumetrica del refrigerante. Il sistema è formato da una unità esterna dotata di compressore e di batteria di scambio in grado di funzionare indifferentemente da condensatore e da evaporatore. Ad essa sono collegate, mediante due tubi nella versione in pompa di calore e a tre tubi nella versione a recupero di calore (ci sono costruttori che usano solo i due tubi per il recupero), una serie di unità interne dotate di ventilatore ad inverter, batteria di scambio termico ad alta efficienza, valvola termostatica di laminazione elettronica e valvola di deviazione a cassetto oppure un cassetto a più distribuzioni nella versione a recupero. Sostanzialmente si tratta di un super-multisplit in cui le unità interne possono lavorare in modo differenziato tra loro sia in termini di limiti di temperatura e anche in modo contemporaneo con alcune unità interne in freddo, per raffrescare il locale, ed altre per riscaldarlo. Nella versione a recupero di calore si tratta quindi di un impianto alternativo al tradizionale quattro tubi a fluido intermedio con gruppi frigoriferi a recupero di calore del tipo polivalenti. Esistono tuttavia anche delle versioni di VRF e VRV in grado di funzionare solo producendo freddo d’estate e caldo d’inverno, come un normale impianto a pompa di calore a fluido intermedio. Questi sistemi sono dotati di soli due tubi, anziché tre come la versione a recupero.
Si compone in via schematica di:
– unità moto condensante/evaporante dotata di uno o più compressori inverter con elevato grado di parzializzazione e quindi di resta
– unità interne che possono essere collegate fino a un massimo di 64 a ciascun sistema (cioè a ciascuna unità esterna);
– collegamento tra le unità esterne ed interne attraverso una coppia di tubazioni di rame.
Nel caso di installazioni che richiedano una potenza superiore a quella fornibile da una singola unità esterna, diventa agevole suddividere la potenzialità richiesta su più unità esterne combinandone le soluzioni, ciascuna delle quali dedicata a una specifica zona dell’edificio. Il sistema è controllato da un unico circuito di trasmissione dati e si comporta per chi lo gestisce come un sistema unico di refrigerazione. Le macchine vengono scelte attraverso delle sigle che variano da costruttore a costruttore che si riferiscono sostanzialmente alla potenza della macchina. La potenza può essere espressa in differenti modi. Per esempio in kW e quindi alcuni costruttori hanno le sigle in multipli di 100 che stanno a significare la potenza in kcal/h decurtata di due zeri. A volte si possono trovare sigle che tengono in considerazione i “cavalli” con un indice di scelta pari a 25.
Le case costruttrici oggi forniscono diversi modelli che vanno dalla versione con unità esterna monoventola (monofase/trifase) fino a 10 HP per arrivare alla versione bi-ventola fino a un massimo 12 HP per arrivare alla versione standard con ventilatore elicoidale in testa per un massimo che si aggira attorno ai 54 HP (150 kW). Quando tutte le unità interne lavorano in raffreddamento, il sistema si comporta come un normale multisplit: l’unità esterna funge da condensatore, quelle interne da evaporatore e vengono utilizzate solamente due delle tre tubazioni. Questo funzionamento è possibile anche nella versione senza recupero a due soli tubi. Se tutte le unità interne lavorano in pompa di calore, il sistema va a funzionare come un normale multisplit in pompa di calore, impiegando due soli tubi con la batteria esterna in funzione di evaporatore e le batterie interne in funzione di condensatore. Anche questo funzionamento è possibile nella versione a due soli tubi senza recupero.
Oggi l’evoluzione tecnologica porta a lavorare anche con la soluzione a moduli, ossia a collettore, dove per ogni collettore di gas/liquido è possibile installare un massimo di 8 unità interne. Questa tipologia mantiene la facilità di installazione dell’impianto idronico, evitando la distribuzione a due tubi con molti punti di saldatura. Quando l’edificio richiede carichi contemporanei opposti, ossia la necessità di fare freddo e caldo contemporaneamente, si passa a unità ad espansione diretta a recupero di calore. La tipologia “tradizionale” prevede la posa di tre tubazioni che poi convergono in un distributore a cassetto, che per semplicità chiameremo Box selettore di flusso, da dove si dipartono le due linee di gas e liquido che alimentano le unità interne. Quando tutte le unità interne lavorano in raffreddamento, il sistema si comporta come un normale multisplit. Qualora parte delle unità interne debbano lavorare in riscaldamento, ma il carico predominante sia quello in raffreddamento, si attua il recupero di energia termica: il vapore surriscaldato in uscita dal condensatore viene inviato parte all’unità esterna, che funge ancora da condensatore, e parte alle unità interne in riscaldamento, attraverso il terzo tubo dell’impianto. Le batterie delle unità interne lavorano anch’esse da condensatore e il liquido ad alta pressione in uscita da esse viene inviato, assieme a quello proveniente dalla batteria dell’unità esterna, alle batterie delle altre unità interne con funzione di evaporatore.
Da segnalare la situazione assolutamente transitoria (non riportata nella figura) in cui il carico tra richiesta di riscaldamento e di condizionamento sia perfettamente bilanciato: l’intera quantità del refrigerante condensa nelle unità funzionanti in riscaldamento ed evapora nelle altre, by-passando la batteria dell’unità esterna. Quando i carichi sono contrapposti, ma la predominanza è in riscaldamento, vi è il recupero di energia frigorifera. Il vapore surriscaldato in uscita dal compressore viene inviato esclusivamente alle batterie delle unità interne, con funzione di condensatore. Il liquido passa le termostatiche elettroniche, abbassandosi di pressione, e viene inviato parte alla batteria dell’unità esterna, che funge da moto evaporatore, e parte alle batterie delle unità in raffreddamento, per poi ricongiungersi, attraverso la terza tubazione, sulla linea di aspirazione del compressore. Anche in questo, vi è la situazione, assolutamente transitoria, in cui il carico tra richiesta di riscaldamento e di condizionamento è perfettamente bilanciato: l’intera quantità del refrigerante condensa nelle unità funzionanti in riscaldamento ed evapora nelle altre, by-passando la batteria dell’unità esterna. Quando, infine, tutte le unità interne lavorano in pompa di calore, il sistema torna a funzionare come un normale multisplit.
Alcune case propongono il recupero di calore usando solo due tubazioni lasciando la ripartizione del carico al Box deviatore di flusso. Nella versione a recupero di calore, le unità terminali sono indipendenti anche dal punto di vista della commutazione caldo/freddo oltre che di temperatura. In questo caso esse sono in grado di scegliere autonomamente se passare, singolarmente attraverso la regolazione, dalla fase di riscaldamento a quella di raffreddamento (e viceversa) al fine di mantenere le condizioni ambiente richieste. Questa soluzione consente il massimo risparmio energetico nella misura in cui provvede a trasferire il calore dalle zone che devono essere raffreddate a quelle che devono essere riscaldate, senza la necessità di dover spendere altra energia sotto forma di lavoro di compressione.
La regolazione dei sistemi VRF e VRV
L’elemento caratteristico del sistema, qualunque sia la versione adottata, risiede nella capacità di variare in modo lineare e direttamente proporzionale al carico (sia in raffreddamento che in riscaldamento) la portata e la temperatura del gas refrigerante in circolazione. Particolarmente sofisticato, quindi, è il sistema di regolazione; la temperatura ambiente è mantenuta costante dal controllo simultaneo delle valvole termostatiche elettroniche di cui sono dotate le singole unità interne e della variazione di portata volumetrica del refrigerante. A seconda del carico richiesto le valvole aprono o chiudono, così da adattare la pressione, quindi la temperatura, di evaporazione (in raffreddamento) e di condensazione (in riscaldamento) ai reali fabbisogni dell’ambiente. La regolazione della portata volumetrica del refrigerante viene fatta variando, con un inverter, il numero di giri del compressore, in base al segnale di ritorno dalle valvole: se le valvole tendono a chiudere, il numero di giri diminuisce, riducendo la portata in tutto il circuito; il contrario se le valvole tendono ad aprire. Ad ogni variazione di carico di raffreddamento o di riscaldamento di ogni ambiente condizionato, corrisponde perciò una variazione di posizione della valvola elettronica di espansione-regolazione dell’unità terminale. La somma delle variazioni di posizione delle valvole induce una variazione di pressione nel circuito frigorifero.
Nel tempo, a intervalli regolari, il microprocessore della motocondensante rileva queste variazioni e le confronta con un valore di riferimento, che è funzione della temperatura dell’aria esterna rilevata dall’apposito termistore. La linea di gestione delle unità interne ed esterne è perciò una linea di comunicazione Bus che permette di realizzare quanto sopra descritto. Oggi il sistema può essere gestito da remoto attraverso una rete Ethernet da un pc o da sistema smart-phone. In figura 7 si riporta quanto descritto per la rete di controllo. Il comando all’inverter viene dato mettendo in parallelo i segnali delle termostatiche elettroniche affinché il numero di giri del compressore, quindi la portata volumetrica di refrigerante, sia regolata in modo da tenere in totale apertura almeno una valvola delle unità interne, generalmente quella dell’unità a maggior carico, garantendo le prestazioni volute con la minor portata di refrigerante possibile. Si ottiene, pertanto, un’ottimizzazione dell’efficienza energetica, che tende a migliorare, a parità di ogni altra condizione, riducendo la portata di refrigerante perché migliorano le pressioni di condensazione e di evaporazione dell’itero ciclo frigorifero. Anche nel funzionamento a recupero di calore, il Box selettore di flusso colloquia con la linea bus per gestire le unità interne in contemporaneo funzionamento estivo e/o invernale. Il sistema che parte da pochi attacchi fino ad una ventina di attacchi trova all’interno delle valvole a due vie comandate dal sistema di controllo in grado di gestire le linee di alta e bassa pressione del gas e la linea del liquido. In figura 8 è riportato il sistema Box selettore di flusso.
Capacità di regolazione del sistema VRF e VRV
Il processo principale di regolazione della capacità termo-frigorifera dei sistemi VRF e VRV sta nella modulazione della capacità della moto-condensante/evaporante attraverso la variazione della frequenza di alimentazione del compressore ad inverter e dei motori dei ventilatori anch’essi inverter. A ogni frequenza di alimentazione imposta dall’inverter, corrisponde perciò una variazione della velocità di rotazione del compressore. E per ogni variazione della velocità di rotazione corrispondono una variazione di portata del refrigerante e una variazione di potenza assorbita. Attualmente si riesce a parzializzare su un range variabile dal 5% circa al 100% della capacità massima erogabile; ne risulta un sistema che si adatta bene ai carichi parziali di raffreddamento e riscaldamento. Le capacità di raffreddamento e di riscaldamento che si ottengono al massimo della parzializzazione sono talmente ridotte da poter alimentare anche un solo terminale della grandezza più piccola tra quelle disponibili. In tali condizioni operative il consumo energetico si riduce all’incirca a quello di uno mono-split di pari capacità termica. I sistemi a refrigerante variabile con inverter permettono perciò di regolare la potenzialità desiderata fino a un minimo del 5%, dopodiché il compressore cesserà di funzionare, ovvero potrà lavorare in regime di on-off. L’applicazione dell’inverter ai motocompressori consente altri vantaggi quali l’avviamento alla frequenza minima, contenendo le correnti di spunto, ed un ampio campo di variazione di superficie evaporante/condensante rispetto a quella nominale aumentandone l’efficienza energetica.
A favore dei sistemi VRF e VRV vi è perciò il sistema di regolazione basato sulla variazione di portata volumetrica del refrigerante: al diminuire del carico richiesto, si riduce anche la portata di refrigerante e, di conseguenza, anche le perdite energetiche lungo le tubazioni. I produttori di sistemi VRF e VRV insistono molto sulle loro prestazioni ai carichi parziali, piuttosto che nelle condizioni nominali di progetto, proprio per quanto esposto sopra. E per il fatto che le condizioni più gravose sia in inverno che in estate accadono poche ore nelle rispettive stagioni, lavorando per più del 70% del tempo ai carichi parziali.
Sistemi VRF e VRV ad acqua e sistemi ibridi
Senza entrare nel merito del loro funzionamento, e senza perdere di generalità, ormai da anni i sistemi VRF e VRV sono prodotti anche con unità da interno del tipo ad acqua, ossia moto-condensanti/evaporanti ad acqua. L’acqua può essere di falda, di mare e/o lago oppure una sorgente geotermica. Il sistema rimane inalterato per la distribuzione delle unità interne e il sistema può essere anche a recupero di calore. Come tipologia di installazione si preferisce l’introduzione di uno scambiatore di calore a piastre. Se le macchine sono più di una, si preferisce la circuitazione idronica in parallelo a ritorno inverso in modo da rendere il circuito abbastanza bilanciato. Sulla resa della singola macchina (generalmente mono compressore ad inverter) abbinata alla sorgente acqua si rimanda alle prestazioni indicate nei numeri precedenti. In situazioni particolari, in centri storici o dove l’unità esterna non può essere installata all’aperto e la soluzione di figura 10 non si può applicare, si segnala la possibilità di installare le unità esterne all’interno degli edifici e realizzare un canotto di espulsione dell’aria, garantendo sempre la corretta presa di aria esterna. Oggi si arriva a gestire fino a cinque livelli di rumorosità delle macchine, garantendo al ventilatore della moto condensante fino a 80 Pa di prevalenza utile.
Un cenno, merita invece la possibilità dei sistemi VRF e VRV più evoluti degli ultimi anni, di realizzare soluzioni per così dire ibride; ossia impianti ad espansione diretta e idronici allo stesso tempo. Molti costruttori, danno la possibilità attraverso dei moduli che chiameremo idronici, di scambiare calore tra il fluido refrigerante e l’acqua di un circuito di riscaldamento a bassa temperatura quale può essere un sistema radiante e ancor più di innalzare la temperatura dell’acqua stessa ai livelli della sanitaria con moduli idronici aventi una piccola pompa di calore in serie alla principale con fluido frigorigeno R134a che ben si presta alle alte temperature di fine compressione. Questo permette ad esempio di avere un impianto di climatizzazione estivo del tipo ad espansione diretta come quelli appena descritti e attraverso dei moduli idronici un sistema che in inverno produce acqua calda a bassa temperatura. L’unico svantaggio è che il sistema lavora con un serbatoio di accumulo.
Alla stessa stregua il modulo idronico può essere composto da una pompa di calore in serie al sistema VRF o VRV in grado attraverso, anche qui, un serbatoio di accumulo di alimentare un sistema di distribuzione di acqua calda sanitaria. Questa versione assai flessibile si inserisce bene in contesti alberghieri, uffici, ambienti commerciali e museali.
In secondo luogo, non vanno sottovalutati gli aspetti legati alla tutela dell’ambiente e alla sicurezza. Indubbiamente, un sistema che oggi usa il fluido frigorigeno R32, al posto del R410a più clima-alterante rispetto al primo, presenta aspetti legati alla sicurezza molto più restrittivi. La scelta oggi di usare R32, fluido con basso GWP ma classificato A2L ossia poco infiammabile, porta a rivedere i sistemi VRF e VRV. Le normative europee sono restrittive e lo spazio non consente una divagazione in merito. Tuttavia giova ricordare come alcuni costruttori per limitare la carica di fluido refrigerante, usano il sistema VRF e VRV per produrre energia frigo-termica e un modulo idronico della stessa tipologia del Box selettore di flusso di figura 8, ma con una pompa di distribuzione.
Occorrere approfondire l’argomento parlando delle distanze che il sistema può impiegare con le tubazioni o della possibilità di applicare al sistema delle unità di trattamento aria sia in termici di UTA-CTA oppure recuperatori di calore, quest’ultimi generalmente entalpici. Anche sistemi di lama d’aria sono facilmente applicabili e gestibili. Altro aspetto delicato, ma gestito dal sistema VRF e VRV sono gli sbrinamenti che ogni costruttore ha risolto in modo soddisfacente arrivando a utilizzare sistemi di accumulo a cambiamento di fase. Il dimensionamento del sistema e la scelta delle tubazioni sono ancora legati alle distanze massime percorribili. Si pensi che oggi si arriva a lunghezze di tubazioni che hanno una massima distanza ammissibile fra unità esterna e interne di circa 170 m e una lunghezza totale che arriva fino a 1000 m, parametri che rendono ancora più flessibile i sistemi VRF e VRV, garantendo dislivelli di 90 m tra unità esterna e unità interne. Per il buon funzionamento del sistema è assolutamente fondamentale che i circuiti frigoriferi siano perfettamente posati da personale specializzato. Sono proprio la distribuzione interna delle linee e le cariche di refrigerante i punti deboli dei VRF e VRV, per due motivi distinti. In primo luogo vi è un aspetto pratico: un’eventuale perdita in qualche punto delle tubazioni diventa estremamente difficile da rilevare.
È vero che una simile eventualità ha scarse probabilità di verificarsi, se l’impianto è installato bene, però una piccola imperfezione può sempre sfuggire ed è giusto considerarla nel valutare l’affidabilità globale del sistema. La varietà di unità interne ne permette l’applicazione in una svariata tipologia di attività. Da segnalare la scelta di unità interne canalizzate a bassa, media e alta prevalenza per applicazioni di interior molto spinte. Discorso a parte meriterebbe l’analisi delle efficienze nominali e stagionali e un confronto critico con i sistemi idronici. Per quanto riguarda la flessibilità di funzionamento e il comfort prodotto, i VRV/VRF non hanno nulla da invidiare ai migliori impianti a quattro tubi. La facilità di manutenzione, di controllo, di ampliamento in un secondo tempo ne fanno un sistema efficiente ed efficace che oggi un progettista e installatore non può sottovalutare.
Condividi l'articolo
Scegli su quale Social Network vuoi condividere